Schieferölgewinnung - Shale oil extraction
![]() Shells experimentelle in situ Schieferölanlage, Piceance Basin , Colorado, USA
| |
Prozesstyp | Chemisch |
---|---|
Industriesektor(en) | Chemische Industrie , Ölindustrie |
Haupttechnologien oder Teilprozesse | Kiviter , Galoter , Petrosix , Fushun , Shell ICP |
Ausgangsmaterial | Ölschiefer |
Produkte) | Schieferöl |
Führende Firmen | Royal Dutch Shell , Eesti Energia , Viru Keemia Grupp , Petrobras , Fushun Mining Group |
Haupteinrichtungen | Fushun-Schieferölpflanze , Narva-Ölpflanze , Petrosix , Stuart-Schieferölpflanze |
Die Schieferölgewinnung ist ein industrielles Verfahren zur unkonventionellen Ölförderung . Dieses Verfahren wandelt Kerogen in Ölschiefer in Schieferöl durch Pyrolyse , Hydrierung oder thermische Auflösung . Das resultierende Schieferöl wird als Heizöl verwendet oder aufbereitet , um die Spezifikationen für Raffinerierohstoffe zu erfüllen, indem Wasserstoff hinzugefügt und Schwefel- und Stickstoffverunreinigungen entfernt werden .
Die Schieferölgewinnung erfolgt in der Regel oberirdisch ( Ex-situ- Verarbeitung), indem der Ölschiefer abgebaut und anschließend in Aufbereitungsanlagen aufbereitet wird . Andere moderne Technologien führen die Verarbeitung unter Tage (Vor-Ort- oder In-Situ- Verarbeitung) durch, indem Wärme angewendet und das Öl über Ölquellen gefördert wird .
Die früheste Beschreibung des Prozesses stammt aus dem 10. Jahrhundert. 1684 erteilte Großbritannien das erste formale Patent für das Extraktionsverfahren. Extraktionsindustrien und Innovationen verbreiteten sich im 19. Jahrhundert. Die Industrie schrumpfte Mitte des 20. Jahrhunderts nach der Entdeckung großer Reserven an konventionellem Öl , aber die hohen Erdölpreise zu Beginn des 21. Jahrhunderts führten zu einem erneuten Interesse, begleitet von der Entwicklung und Erprobung neuerer Technologien.
Seit 2010 sind in Estland , Brasilien und China bedeutende, seit langem bestehende Förderindustrien tätig . Seine wirtschaftliche Tragfähigkeit setzt in der Regel einen Mangel an lokal verfügbarem Rohöl voraus. Auch nationale Fragen der Energiesicherheit haben bei seiner Entwicklung eine Rolle gespielt. Kritiker der Schieferölförderung stellen Fragen zu Umweltmanagementthemen wie Abfallentsorgung, extensiver Wassernutzung, Abwassermanagement und Luftverschmutzung.
Geschichte
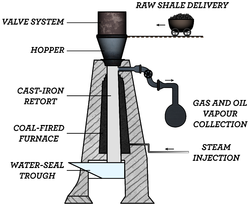
Im 10. Jahrhundert schrieb der arabische Arzt Masawaih al-Mardini (Mesue der Jüngere) über seine Versuche zur Gewinnung von Öl aus „einer Art bituminösem Schiefer“. Das erste Patent zur Gewinnung von Schieferöl wurde 1684 von der britischen Krone an drei Personen erteilt, die "einen Weg gefunden hatten, große Mengen Pech, Teer und Oyl aus einer Art Stein zu extrahieren und herzustellen". Die moderne industrielle Gewinnung von Schieferöl entstand in Frankreich mit der Implementierung eines Verfahrens, das 1838 von Alexander Selligue erfunden und ein Jahrzehnt später in Schottland mit einem von James Young erfundenen Verfahren verbessert wurde . Im späten 19. Jahrhundert wurden Anlagen in Australien, Brasilien, Kanada und den Vereinigten Staaten gebaut. Die Erfindung der Pumpherston-Retorte im Jahr 1894 , die viel weniger auf Kohlewärme angewiesen war als ihre Vorgänger, markierte die Trennung der Ölschieferindustrie von der Kohleindustrie.
China ( Mandschurei ), Estland, Neuseeland , Südafrika , Spanien , Schweden und die Schweiz begannen Anfang des 20. Jahrhunderts mit der Gewinnung von Schieferöl. Rohölfunde in Texas in den 1920er Jahren und im Nahen Osten Mitte des 20. Jahrhunderts brachten jedoch die meisten Ölschieferindustrien zum Erliegen. 1944 begannen die USA im Rahmen ihres Programms für synthetische flüssige Brennstoffe wieder mit der Schieferölförderung . Diese Industrien setzten sich fort, bis die Ölpreise in den 1980er Jahren stark fielen. Die letzte Ölschiefer-Retorte in den USA, die von Unocal Corporation betrieben wurde , wurde 1991 geschlossen. Das US-Programm wurde 2003 wieder aufgenommen, gefolgt von einem kommerziellen Pachtprogramm im Jahr 2005, das die Förderung von Ölschiefer und Ölsanden auf Bundesland in Übereinstimmung mit den Energiepolitisches Gesetz von 2005 .
Seit 2010 wird Schieferöl in Estland, Brasilien und China gefördert. Im Jahr 2008 produzierten ihre Industrien etwa 930.000 Tonnen (17.700 Barrel pro Tag) Schieferöl. Australien, die USA und Kanada haben Schieferölgewinnungstechniken anhand von Demonstrationsprojekten getestet und planen eine kommerzielle Umsetzung; Marokko und Jordanien haben angekündigt, dasselbe zu tun. Nur vier Verfahren werden kommerziell genutzt: Kiviter , Galoter , Fushun und Petrosix .
Verarbeitungsprinzipien
Schieferöl Extraktionsprozess zersetzt Ölschiefer und wandelt seine Kerogen in Schieferöl-eine Mineralöl -ähnlichen synthetisches Rohöl Öl. Der Prozess wird durch Pyrolyse , Hydrierung oder thermische Auflösung durchgeführt . Die Effizienz von Extraktionsprozessen wird oft bewertet, indem ihre Ausbeuten mit den Ergebnissen eines Fischer-Assays verglichen werden, der an einer Probe des Schiefers durchgeführt wurde.
Die älteste und gebräuchlichste Extraktionsmethode ist die Pyrolyse (auch Retorten oder destruktive Destillation genannt ). Bei diesem Prozess wird Ölschiefer in Abwesenheit von Sauerstoff erhitzt, bis sich sein Kerogen in kondensierbare Schieferöldämpfe und nicht kondensierbares brennbares Ölschiefergas zersetzt . Öldämpfe und Ölschiefergas werden dann gesammelt und gekühlt, wodurch das Schieferöl kondensiert . Darüber hinaus entsteht bei der Ölschieferverarbeitung Altölschiefer, bei dem es sich um einen festen Rückstand handelt. Verbrauchter Schiefer besteht aus anorganischen Verbindungen ( Mineralien ) und Kohle – einem kohlenstoffhaltigen Rückstand, der aus Kerogen gebildet wird. Beim Verbrennen der Holzkohle aus dem verbrauchten Schiefer entsteht Ölschieferasche. Verbrauchter Schiefer und Schieferasche können als Zutaten in der Zement- oder Ziegelherstellung verwendet werden. Die Zusammensetzung des Ölschiefers kann dem Extraktionsprozess durch die Rückgewinnung von Nebenprodukten wie Ammoniak , Schwefel , aromatische Verbindungen , Pech , Asphalt und Wachse einen Mehrwert verleihen .
Das Erhitzen des Ölschiefers auf Pyrolysetemperatur und das Vervollständigen der endothermen Kerogenzersetzungsreaktionen erfordern eine Energiequelle. Einige Technologien verbrennen andere fossile Brennstoffe wie Erdgas, Öl oder Kohle, um diese Wärme zu erzeugen, und experimentelle Methoden haben zu diesem Zweck Elektrizität, Radiowellen , Mikrowellen oder reaktive Flüssigkeiten verwendet. Zwei Strategien werden verwendet, um den externen Wärmeenergiebedarf zu reduzieren oder sogar zu eliminieren: Das bei der Pyrolyse erzeugte Ölschiefergas und die Kohlenebenprodukte können als Energiequelle verbrannt werden, und die in heißem gebrauchtem Ölschiefer und Ölschieferasche enthaltene Wärme kann zum Vorwärmen des Rohölschiefers verwendet werden.
Für die Ex-situ- Verarbeitung wird Ölschiefer in kleinere Stücke zerkleinert, wodurch die Oberfläche für eine bessere Extraktion vergrößert wird. Die Temperatur, bei der die Zersetzung von Ölschiefer stattfindet, hängt von der Zeitskala des Prozesses ab. Bei Ex-situ- Retortenprozessen beginnt sie bei 300 °C (570 °F) und verläuft bei höheren Temperaturen schneller und vollständiger. Die produzierte Ölmenge ist am höchsten, wenn die Temperatur zwischen 480 und 520 °C (900 und 970 °F) liegt. Das Verhältnis von Ölschiefergas zu Schieferöl steigt im Allgemeinen zusammen mit den Retortentemperaturen. Bei einem modernen In-situ- Prozess, der mehrere Monate des Erhitzens in Anspruch nehmen kann, kann die Zersetzung bei Temperaturen von bis zu 250 °C (480 °F) durchgeführt werden. Temperaturen unter 600 °C (1.110 °F) sind vorzuziehen, da dies die Zersetzung von Kalkstein und Dolomit im Gestein verhindert und dadurch den Kohlendioxidausstoß und den Energieverbrauch begrenzt.
Hydrierung und thermische Auflösung (reaktive Fluidprozesse) extrahieren das Öl unter Verwendung von Wasserstoffspendern , Lösungsmitteln oder einer Kombination davon. Die thermische Auflösung beinhaltet die Anwendung von Lösungsmitteln bei erhöhten Temperaturen und Drücken, wodurch die Ölförderung durch das Cracken der gelösten organischen Stoffe erhöht wird . Unterschiedliche Verfahren produzieren Schieferöl mit unterschiedlichen Eigenschaften.
Klassifizierung der Extraktionstechnologien
Branchenanalysten haben mehrere Klassifizierungen der Technologien erstellt, die zur Gewinnung von Schieferöl aus Ölschiefer verwendet werden.
Nach Verfahrensprinzipien : Basierend auf der Behandlung von Rohölschiefer durch Hitze und Lösungsmittel werden die Verfahren als Pyrolyse, Hydrierung oder thermische Auflösung klassifiziert.
Nach Standort : Eine häufig verwendete Unterscheidung berücksichtigt, ob die Verarbeitung über oder unter der Erde erfolgt, und klassifiziert die Technologien grob in ex situ (versetzt) oder in situ (vor Ort). Bei der Ex-situ- Verarbeitung, auch als oberirdisches Retorting bekannt , wird der Ölschiefer entweder unter Tage oder an der Oberfläche abgebaut und dann zu einer Verarbeitungsanlage transportiert. Im Gegensatz dazu wird bei der In-situ- Verarbeitung das Kerogen noch in Form einer Ölschieferlagerstätte umgewandelt und anschließend über Ölquellen gefördert , wo es wie herkömmliches Rohöl nachsteigt. Im Gegensatz zur Ex-situ- Verarbeitung umfasst sie keinen Abbau oder die oberirdische Entsorgung von verbrauchtem Ölschiefer, da verbrauchter Ölschiefer unter der Erde bleibt.
Durch Erhitzungsmethode : Die Methode der Wärmeübertragung von Verbrennungsprodukten auf den Ölschiefer kann als direkt oder indirekt klassifiziert werden. Während Verfahren, bei denen Verbrennungsprodukte mit dem Ölschiefer in der Retorte in Kontakt kommen, als direkt klassifiziert werden , werden Verfahren, die Materialien außerhalb der Retorte verbrennen, um ein anderes Material zu erhitzen, das mit dem Ölschiefer in Kontakt kommt, als indirekt bezeichnet
Nach Wärmeträger : Basierend auf dem Material, das verwendet wird, um dem Ölschiefer Wärmeenergie zuzuführen, wurden die Verarbeitungstechnologien in Gaswärmeträger, feste Wärmeträger, Wandleitung, reaktive Flüssigkeit und volumetrische Heizmethoden eingeteilt. Wärmeträgermethoden können in direkt oder indirekt unterteilt werden.
Die folgende Tabelle zeigt die Extraktionstechnologien unterteilt nach Heizmethode, Wärmeträger und Standort ( in situ oder ex situ ).
Klassifizierung der Verarbeitungstechnologien nach Heizmethode und Standort (nach Alan Burnham) | ||
---|---|---|
Heizmethode | Oberirdisch ( ex situ ) | Untergrund ( in situ ) |
Verbrennungs | Gasverbrennung , NTU , Kiviter , Fushun , Union A , Paraho Direkt , Superior - Direkt | Occidental Petroleum MIS , LLNL RISE , Geokinetics Horizontal , Rio Blanco |
Heiße recycelte Feststoffe (inerter oder verbrannter Schiefer) |
Alberta Taciuk , Galoter , Enefit , Lurgi-Ruhrgas , TOSCO II , Chevron STB , LLNL HRS , Shell Spher , KENTORT II |
– |
Leitung durch eine Wand (verschiedene Brennstoffe) |
Pumpherston , Fischer Assay , Oil-Tech , EcoShale In-Capsule , Verbrennungsressourcen | Shell ICP (primäre Methode), American Shale Oil CCR , IEP Geothermic Fuel Cell |
Extern erzeugtes Heißgas | PetroSIX , Union B , Paraho Indirect , Superior Indirect , Syntec (Smith-Verfahren) | Chevron CRUSH , Omnishale , MWE IGE |
Reaktive Flüssigkeiten | IGT Hytort (Hochdruck H 2 ), Donor-Lösungsmittel-Verfahren Rendall Process Chattanooga Wirbelschichtreaktor | Shell-ICP (einige Ausführungsformen) |
Volumetrische Erwärmung | – | Radiowellen-, Mikrowellen- und Stromprozesse |
Nach Rohölschiefer-Partikelgröße : Die verschiedenen Ex-situ- Verarbeitungstechnologien können durch die Größe der Ölschiefer-Partikel, die in die Retorten eingespeist werden, unterschieden werden. In der Regel verarbeiten Gaswärmeträgertechnologien Ölschieferklumpen mit einem Durchmesser von 10 bis 100 Millimetern (0,4 bis 3,9 Zoll), während feste Wärmeträger- und Wandleitungstechnologien Feinstpartikel verarbeiten, die Partikel mit einem Durchmesser von weniger als 10 Millimetern (0,4 Zoll) sind .
Nach Retortenorientierung : "Ex-situ"-Technologien werden manchmal als vertikal oder horizontal klassifiziert. Vertikale Retorten sind normalerweise Schachtöfen, in denen sich ein Schieferbett durch die Schwerkraft von oben nach unten bewegt. Horizontale Retorten sind normalerweise horizontal rotierende Trommeln oder Schnecken, bei denen sich Schiefer von einem Ende zum anderen bewegt. In der Regel verarbeiten vertikale Retorten Klumpen mit einem gasförmigen Wärmeträger, während horizontale Retorten Feinteile mit festem Wärmeträger verarbeiten.
Nach Komplexität der Technologie : In-situ- Technologien werden normalerweise entweder als echte in-situ- Prozesse oder als modifizierte in-situ- Prozesse klassifiziert . Echte in-situ- Prozesse beinhalten weder den Abbau noch die Zerkleinerung des Ölschiefers. Modifizierte in-situ- Prozesse beinhalten das Bohren und das Aufbrechen der Ziel-Ölschiefer-Lagerstätte, um Hohlräume in der Lagerstätte zu erzeugen. Die Hohlräume ermöglichen einen besseren Durchfluss von Gasen und Flüssigkeiten durch die Lagerstätte, wodurch Volumen und Qualität des geförderten Schieferöls erhöht werden.
Ex-situ- Technologien
Verbrennungs
Verbrennungstechnologien verbrennen Materialien (typischerweise Holzkohle und Ölschiefergas) in einer vertikalen Schachtretorte, um Wärme für die Pyrolyse zu liefern. Typischerweise werden Rohölschieferpartikel zwischen 12 Millimeter (0,5 Zoll) und 75 Millimeter (3,0 Zoll) in die Oberseite der Retorte eingespeist und von den aufsteigenden heißen Gasen erhitzt, die durch den absteigenden Ölschiefer strömen, wodurch die Zersetzung von das Kerogen bei etwa 500 °C (932 °F). Schieferölnebel, freigesetzte Gase und gekühlte Verbrennungsgase werden von der Oberseite der Retorte entfernt und dann zu einer Trennanlage transportiert. Kondensiertes Schieferöl wird gesammelt, während nicht kondensierbares Gas recycelt und zum Aufheizen der Retorte verwendet wird. Im unteren Teil der Retorte wird Luft zur Verbrennung eingespritzt, die den verbrauchten Ölschiefer und die Gase auf 700 °C (1.292 °F) bis 900 °C (1.650 °F) erhitzt. Kaltes rückgeführtes Gas kann in den Boden der Retorte eintreten, um die Schieferasche zu kühlen. Die Prozesse Union A und Superior Direct weichen von diesem Muster ab. Beim Union A-Verfahren wird Ölschiefer durch den Boden der Retorte gefördert und von einer Pumpe nach oben befördert. Beim Superior Direct-Verfahren wird Ölschiefer in einer horizontalen, segmentierten, Donut-förmigen Wanderrostretorte verarbeitet .
Verbrennungstechnologien wie Paraho Direct sind thermisch effizient , da die Verbrennung von Holzkohle auf dem verbrauchten Schiefer und die aus der Schieferasche und den entstehenden Gasen gewonnene Wärme den gesamten Wärmebedarf der Retorte decken kann. Diese Technologien können 80–90 % der Fischer-Assay-Ausbeute erreichen. Zwei etablierte Schieferölindustrien verwenden Verbrennungstechnologien: Kiviter-Prozessanlagen werden in Estland seit den 1920er Jahren kontinuierlich betrieben, und eine Reihe chinesischer Unternehmen betreiben Fushun-Prozessanlagen .
Gemeinsame Nachteile von Verbrennungstechnologien sind, dass das brennbare Ölschiefergas durch Verbrennungsgase verdünnt wird und Partikel, die kleiner als 10 Millimeter (0,4 Zoll) sind, nicht verarbeitet werden können. Eine ungleichmäßige Gasverteilung in der Retorte kann zu Verstopfungen führen, wenn heiße Stellen dazu führen, dass Partikel verschmelzen oder zerfallen.
Heiß recycelte Feststoffe
Heißrecycling-Feststofftechnologien liefern Wärme an den Ölschiefer, indem sie heiße Feststoffpartikel – typischerweise Ölschieferasche – recyceln. Diese Technologien verwenden normalerweise Drehofen- oder Wirbelschicht- Retorten, die von feinen Ölschieferpartikeln gespeist werden, die im Allgemeinen einen Durchmesser von weniger als 10 Millimeter (0,4 Zoll) haben; einige Technologien verwenden sogar Partikel, die kleiner als 2,5 Millimeter sind. Die recycelten Partikel werden in einer separaten Kammer oder einem separaten Gefäß auf etwa 800 °C (1.470 °F) erhitzt und dann mit dem Rohölschiefer vermischt, damit sich der Schiefer bei etwa 500 °C (932 °F) zersetzt. Öldampf und Schieferölgas werden von den Feststoffen getrennt und gekühlt, um zu kondensieren und das Öl zu sammeln. Die aus den Verbrennungsgasen und der Schieferasche gewonnene Wärme kann verwendet werden, um den Rohölschiefer zu trocknen und vorzuwärmen, bevor er mit den heißen Recyclingfeststoffen vermischt wird.
In den Galoter und enefit Verfahren wird die verbrauchte Ölschiefers in einem separaten Ofen verbrannt , und die sich ergebende heiße Asche aus dem Verbrennungsgas abgetrennt und mit Ölschiefer Teilchen in einem Drehofen vermischt. Verbrennungsgase aus dem Ofen werden verwendet, um den Ölschiefer in einem Trockner zu trocknen, bevor er mit heißer Asche vermischt wird. Der TOSCO II-Prozess verwendet Keramikkugeln anstelle von Schieferasche als heiße recycelte Feststoffe. Das Unterscheidungsmerkmal des Alberta-Taciuk-Prozesses (ATP) besteht darin, dass der gesamte Prozess in einem einzigen rotierenden horizontalen Mehrkammer-Gefäß stattfindet.
Da die heißen Recycling-Feststoffe in einem separaten Ofen erhitzt werden, wird das Ölschiefergas aus diesen Technologien nicht mit Verbrennungsabgas verdünnt. Ein weiterer Vorteil besteht darin, dass die kleinsten Partikel, die die Retorte verarbeiten kann, unbegrenzt sind, sodass das gesamte zerkleinerte Futter verwendet werden kann. Ein Nachteil besteht darin, dass mehr Wasser verwendet wird, um die resultierende feinere Schieferasche zu verarbeiten.
Leitung durch eine Wand
Diese Technologien übertragen Wärme auf den Ölschiefer, indem sie ihn durch die Retortenwand leiten. Das Schieferfutter besteht normalerweise aus feinen Partikeln. Ihr Vorteil liegt darin, dass Retortendämpfe nicht mit Verbrennungsabgasen kombiniert werden. Der Verbrennungsressourcenprozess verwendet einen wasserstoffbefeuerten Drehofen, in dem heißes Gas durch einen äußeren Ringraum zirkuliert wird . Die gestufte elektrisch beheizte Retorte von Oil-Tech besteht aus einzelnen, miteinander verbundenen Heizkammern, die übereinander gestapelt sind. Sein Hauptvorteil liegt in seinem modularen Design , das seine Tragbarkeit und Anpassungsfähigkeit verbessert. Der EcoShale In-Capsule-Prozess von Red Leaf Resources kombiniert den Tagebau mit einer Niedrigtemperatur-Heizmethode, die den In-situ- Prozessen ähnelt, indem er innerhalb der Grenzen einer Erdstruktur betrieben wird. Ein heißes Gas, das durch parallele Rohre zirkuliert, erhitzt den Ölschieferschutt. Eine Installation innerhalb des durch den Bergbau entstandenen Leerraums würde eine schnelle Rekultivierung der Topographie ermöglichen. Ein allgemeiner Nachteil der Wärmeleitungs-durch-Wand-Technologien besteht darin, dass die Retorten aufgrund der resultierenden großen Menge an wärmeleitenden Wänden aus Hochtemperaturlegierungen im Maßstab teurer sind.
Extern erzeugtes Heißgas
Im Allgemeinen ähneln fremderzeugte Heißgastechnologien den Verbrennungstechnologien darin, dass sie auch Ölschieferbrocken in vertikalen Schachtöfen verarbeiten. Bezeichnenderweise wird die Wärme bei diesen Technologien jedoch durch außerhalb des Retortenbehälters erhitzte Gase geliefert, und daher werden die Retortendämpfe nicht mit Verbrennungsabgasen verdünnt. Die Petrosix und Paraho Indirect verwenden diese Technologie. Abgesehen davon, dass keine feinen Partikel als Beschickung akzeptiert werden, nutzen diese Technologien nicht die potentielle Wärme der Verbrennung der Kohle auf dem verbrauchten Schiefer und müssen daher wertvollere Brennstoffe verbrennen. Aufgrund der fehlenden Verbrennung des verbrauchten Schiefers überschreitet der Ölschiefer jedoch nicht 500 °C (932 °F), und bei einigen Ölschiefern kann eine signifikante Zersetzung von Karbonatmineralen und die anschließende CO 2 -Erzeugung vermieden werden. Außerdem sind diese Technologien tendenziell stabiler und leichter zu kontrollieren als Technologien mit interner Verbrennung oder heißem Feststoff-Recycling.
Reaktive Flüssigkeiten
Kerogen ist fest mit dem Schiefer verbunden und widersteht der Auflösung durch die meisten Lösungsmittel . Trotz dieser Einschränkung wurde die Extraktion mit besonders reaktiven Fluiden getestet, einschließlich solcher in einem überkritischen Zustand. Reaktive Fluidtechnologien eignen sich für die Verarbeitung von Ölschiefer mit niedrigem Wasserstoffgehalt. In diesen Technologien Wasserstoffgas (H 2 ) oder Wasserstoff - Donatoren (Chemikalien , die Wasserstoff bei chemischen Reaktionen spenden) reagieren mit Koks Vorläufern (chemischen Strukturen im Ölschiefer , die während der Retorten zu bilden char anfällig sind , aber noch nicht geschehen). Zu den reaktiven Fluidtechnologien gehören das IGT Hytort (Hochdruck-H 2 )-Verfahren, Donator-Lösungsmittel-Verfahren und der Chattanooga-Wirbelschichtreaktor . Im IGT Hytort wird Ölschiefer in einer Hochdruck-Wasserstoffumgebung verarbeitet. Der Chattanooga-Prozess verwendet einen Wirbelschichtreaktor und eine zugehörige wasserstoffbefeuerte Heizung zum thermischen Cracken und Hydrieren von Ölschiefer . Laborergebnisse zeigen, dass mit diesen Technologien oft deutlich höhere Ölausbeuten erzielt werden können als mit Pyrolyseverfahren. Nachteile sind die zusätzlichen Kosten und die Komplexität der Wasserstoffproduktion und der Hochdruck-Retortenbehälter.
Plasmavergasung
Zur Öl-Schiefer-Vergasung wurden mehrere experimentelle Tests unter Verwendung von Plasmatechnologien durchgeführt . Bei diesen Technologien wird Ölschiefer mit Radikalen ( Ionen ) bombardiert . Die Reste knacken Kerogen Moleküle bilden synthetisches Gas und Öl. Als Plasmagas werden Luft, Wasserstoff oder Stickstoff verwendet und Verfahren können in einem Lichtbogen- , Plasmalichtbogen- oder Plasmaelektrolysemodus ablaufen. Der Hauptvorteil dieser Technologien ist die Verarbeitung ohne Wasser.
In-situ- Technologien
In-situ- Technologien erhitzen Ölschiefer unter der Erde, indem heiße Flüssigkeiten in die Gesteinsformation injiziert werden oder indem lineare oder planare Heizquellen gefolgt von Wärmeleitung und Konvektion verwendet werden, um die Wärme im Zielgebiet zu verteilen. Schieferöl wird dann durch vertikale Bohrlöcher in der Formation gewonnen. Diese Technologien sind potenziell in der Lage, mehr Schieferöl aus einer bestimmten Landfläche zu gewinnen als herkömmliche Ex-situ- Verarbeitungstechnologien, da die Bohrlöcher größere Tiefen erreichen können als Tagebauminen. Sie bieten die Möglichkeit, Schieferöl aus minderwertigen Lagerstätten zu gewinnen, die mit herkömmlichen Abbautechniken nicht gefördert werden konnten.
Während des Zweiten Weltkriegs wurde in Deutschland ein modifiziertes in-situ- Extraktionsverfahren ohne nennenswerten Erfolg eingeführt. Einer der frühesten erfolgreichen in-situ- Prozesse war die unterirdische Vergasung durch elektrische Energie ( Ljungström- Methode) – ein Prozess, der zwischen 1940 und 1966 zur Schieferölförderung bei Kvarntorp in Schweden genutzt wurde. Vor den 1980er Jahren wurden in den Vereinigten Staaten viele Variationen des In-situ- Prozesses erforscht. Das erste modifizierte In-situ -Ölschiefer-Experiment in den Vereinigten Staaten wurde 1972 von Occidental Petroleum in Logan Wash, Colorado, durchgeführt. Neuere Technologien werden erforscht, die eine Vielzahl von Wärmequellen und Wärmeabgabesystemen verwenden.
Wandleitung

Wandleitung in situ - Technologien nutzen Heizelemente oder Rohrleitungen innerhalb der Ölschieferformation platziert erhitzt wird . Der Shell-In-situ-Umwandlungsprozess (Shell ICP) verwendet elektrische Heizelemente, um die Ölschieferschicht über einen Zeitraum von etwa vier Jahren auf zwischen 340 und 370 °C (650 und 700 °F) zu erhitzen. Der Verarbeitungsbereich ist vom umgebenden Grundwasser durch eine Gefrierwand isoliert, die aus Brunnen besteht, die mit einer zirkulierenden supergekühlten Flüssigkeit gefüllt sind. Nachteile dieses Verfahrens sind der hohe Stromverbrauch, der hohe Wasserverbrauch und die Gefahr der Grundwasserverschmutzung . Das Verfahren wurde seit Anfang der 1980er Jahre auf dem Mahogany-Testgelände im Piceance-Becken getestet . 270 Kubikmeter (1.700 bbl) Öl wurden im Jahr 2004 auf einem 9 mal 12 Meter großen Testgebiet gefördert.
Bei dem von American Shale Oil vorgeschlagenen CCR-Verfahren wird überhitzter Dampf oder ein anderes Wärmeübertragungsmedium durch eine Reihe von Rohren zirkuliert, die unter der zu extrahierenden Ölschieferschicht angeordnet sind. Das System kombiniert horizontale Bohrlöcher, durch die Dampf geleitet wird, und vertikale Bohrlöcher, die sowohl eine vertikale Wärmeübertragung durch Rückfluss von umgewandeltem Schieferöl als auch ein Mittel zum Sammeln der produzierten Kohlenwasserstoffe bieten . Die Wärmeversorgung erfolgt in der Anfangsphase durch die Verbrennung von Erdgas oder Propan und später durch Ölschiefergas.
Der von Independent Energy Partners vorgeschlagene Geothermic Fuels Cells Process (IEP GFC) fördert Schieferöl durch die Nutzung eines Hochtemperatur- Brennstoffzellenstapels . Die Zellen, die in der Ölschieferformation platziert sind, werden während einer Aufwärmphase mit Erdgas und anschließend mit Ölschiefergas, das durch seine eigene Abwärme erzeugt wird, betrieben .
Extern erzeugtes Heißgas
Extern erzeugte Heißgas- In-situ- Technologien verwenden heiße Gase, die über Tage erhitzt und dann in die Ölschieferformation injiziert werden. Der Chevron CRUSH- Prozess, der von der Chevron Corporation in Zusammenarbeit mit dem Los Alamos National Laboratory erforscht wurde , injiziert erhitztes Kohlendioxid über Bohrlöcher in die Formation und erwärmt die Formation durch eine Reihe von horizontalen Brüchen, durch die das Gas zirkuliert. General Synfuels International hat das Omnishale-Verfahren vorgeschlagen, bei dem überhitzte Luft in die Ölschieferformation eingespritzt wird . Das In-Situ-Dampfextraktionsverfahren von Mountain West Energy verwendet ähnliche Prinzipien der Injektion von Hochtemperaturgas.
ExxonMobil Elektrofrak
ExxonMobil ‚s in situ - Technik ( ExxonMobil Electrofrac ) verwendet elektrische Heizung mit den Elementen der beiden Wandleitung und volumetrischen Heizverfahren. Es injiziert ein elektrisch leitfähiges Material wie kalzinierten Petrolkoks in die in der Ölschieferformation erzeugten hydraulischen Brüche, die dann ein Heizelement bilden. Heizbrunnen werden in einer parallelen Reihe mit einem zweiten horizontalen Brunnen platziert, der sie an ihrer Spitze schneidet. Dadurch können an beiden Enden entgegengesetzte elektrische Ladungen angelegt werden.
Volumetrische Erwärmung
Das Illinois Institute of Technology entwickelte Ende der 1970er Jahre das Konzept der volumetrischen Erhitzung von Ölschiefer unter Verwendung von Radiowellen (Radiofrequenzverarbeitung). Diese Technologie wurde vom Lawrence Livermore National Laboratory weiterentwickelt . Ölschiefer wird durch vertikale Elektrodenanordnungen erhitzt . Tiefere Volumina könnten mit langsameren Heizraten durch Installationen mit einem Abstand von mehreren zehn Metern verarbeitet werden. Das Konzept geht von einer Radiofrequenz aus, bei der die Eindringtiefe viele zehn Meter beträgt, wodurch die für die konduktive Erwärmung erforderlichen thermischen Diffusionszeiten überwunden werden. Zu den Nachteilen zählen der hohe Strombedarf und die Möglichkeit, dass Grundwasser oder Kohle übermäßig viel Energie absorbieren. Die Hochfrequenzverarbeitung in Verbindung mit kritischen Flüssigkeiten wird von Raytheon zusammen mit CF Technologies entwickelt und von Schlumberger getestet .
Mikrowellenerwärmungstechnologien basieren auf den gleichen Prinzipien wie Radiowellenerwärmung, obwohl angenommen wird, dass Radiowellenerwärmung eine Verbesserung gegenüber Mikrowellenerwärmung darstellt, da ihre Energie weiter in die Ölschieferformation eindringen kann. Der Mikrowellenheizprozess wurde von der Global Resource Corporation getestet . Electro-Petroleum schlägt eine elektrisch verbesserte Ölgewinnung durch den Durchgang von Gleichstrom zwischen Kathoden in Förderbohrlöchern und Anoden vor, die sich entweder an der Oberfläche oder in der Tiefe in anderen Bohrlöchern befinden. Der Stromdurchgang durch die Ölschieferformation führt zu einer ohmschen Jouleschen Erwärmung .
Wirtschaft
Die dominierende Frage bei der Schieferölproduktion ist, unter welchen Bedingungen Schieferöl wirtschaftlich rentabel ist. Nach Angaben des Energieministeriums der Vereinigten Staaten betragen die Kapitalkosten für einen Ex-situ- Verarbeitungskomplex von 100.000 Barrel pro Tag (16.000 m 3 /d) 3 bis 10 Milliarden US-Dollar. Die verschiedenen Versuche, Ölschiefervorkommen zu erschließen, waren nur dann erfolgreich, wenn die Produktionskosten für Schieferöl in einer bestimmten Region niedriger sind als der Preis für Erdöl oder seine anderen Ersatzstoffe. Laut einer von der RAND Corporation durchgeführten Umfrage würden die Kosten für die Produktion von Schieferöl in einem hypothetischen Oberflächen-Retortenkomplex in den Vereinigten Staaten (bestehend aus einer Mine, einer Retortenanlage, einer Aufbereitungsanlage , unterstützenden Versorgungsunternehmen und der Rückgewinnung von Altölschiefer) in eine Spanne von 70–95 USD pro Barrel (440–600 USD/m 3 ), angepasst an die Werte von 2005. Unter der Annahme einer schrittweisen Steigerung der Produktion nach dem Beginn der kommerziellen Produktion prognostiziert die Analyse eine schrittweise Reduzierung der Verarbeitungskosten auf 30–40 USD pro Barrel (190–250 USD/m 3 ) nach Erreichen des Meilensteins von 1 Milliarde Barrel (160 × 10 6 m .). 3 )). Das Energieministerium der Vereinigten Staaten schätzt, dass die Ex-situ- Verarbeitung bei anhaltenden durchschnittlichen Weltölpreisen von über 54 USD pro Barrel wirtschaftlich wäre und die In-situ- Verarbeitung bei Preisen über 35 USD pro Barrel wirtschaftlich wäre. Diese Schätzungen gehen von einer Rücklaufquote von 15 % aus. Royal Dutch Shell gab im Jahr 2006 bekannt, dass seine Shell ICP-Technologie einen Gewinn erzielen würde, wenn der Rohölpreis über 30 USD pro Barrel (190 USD/m 3 ) liegt, während einige Technologien bei voller Produktion eine Rentabilität bei Ölpreisen von sogar unter 20 USD pro Barrel behaupten Barrel (130 $/m 3 ).
Um die Effizienz der Ölschiefer-Retortenbehandlung und damit die Rentabilität der Schieferölproduktion zu erhöhen, haben Forscher mehrere Co-Pyrolyseverfahren vorgeschlagen und getestet, bei denen andere Materialien wie Biomasse , Torf , Abfallbitumen oder Gummi- und Kunststoffabfälle sterilisiert werden zusammen mit dem Ölschiefer. Einige modifizierte Technologien schlagen vor, eine Wirbelschichtretorte mit einem zirkulierten Wirbelschichtofen zum Verbrennen der Nebenprodukte der Pyrolyse (Kohlenkohle und Ölschiefergas) zu kombinieren und dadurch die Ölausbeute zu verbessern, den Durchsatz zu erhöhen und die Retortenzeit zu verkürzen.
Andere Möglichkeiten zur Verbesserung der Wirtschaftlichkeit der Schieferölförderung könnten darin bestehen, die Größe des Betriebs zu erhöhen, um Skaleneffekte zu erzielen , Ölschiefer zu verwenden, der ein Nebenprodukt des Kohlebergbaus wie bei Fushun China ist, und Spezialchemikalien wie von Viru Keemia zu produzieren Grupp in Estland, erzeugt Strom aus der Abwärme und verarbeitet hochwertigen Ölschiefer, der mehr Öl pro verarbeitetem Schiefer liefert.
Ein mögliches Maß für die Lebensfähigkeit von Ölschiefer als Energiequelle liegt im Verhältnis der Energie des geförderten Öls zu der bei seiner Gewinnung und Verarbeitung aufgewendeten Energie (Energy Returned on Energy Invested, kurz EROEI ). Eine Studie aus dem Jahr 1984 schätzte den EROEI der verschiedenen bekannten Ölschiefervorkommen auf 0,7–13,3; Einige Unternehmen und neuere Technologien geben einen EROEI zwischen 3 und 10 an. Laut World Energy Outlook 2010 beträgt der EROEI der Ex-situ- Verarbeitung typischerweise 4 bis 5, während er bei der In-situ- Verarbeitung sogar nur 2 betragen kann.
Um den EROEI zu erhöhen, wurden mehrere kombinierte Technologien vorgeschlagen. Dazu zählen die Nutzung von Prozessabwärme, zB Vergasung oder Verbrennung des Restkohlenstoffs (Kohlenstoff), sowie die Nutzung von Abwärme aus anderen Industrieprozessen wie der Kohlevergasung und der Kernkrafterzeugung .
In Regionen, in denen Wasser eine knappe Ressource ist, ist der Wasserbedarf von Extraktionsprozessen ein zusätzlicher wirtschaftlicher Aspekt.
Umwelterwägungen
Der Abbau von Ölschiefer ist mit einer Reihe von Umweltauswirkungen verbunden, die im Tagebau stärker ausgeprägt sind als im Untertagebergbau. Dazu gehören saure Drainage durch die plötzliche schnelle Exposition und anschließende Oxidation von ehemals verschütteten Materialien, der Eintrag von Metallen einschließlich Quecksilber in Oberflächen- und Grundwasser, erhöhte Erosion , Schwefelgasemissionen und Luftverschmutzung durch die Bildung von Partikeln während der Verarbeitung , Transport und unterstützende Aktivitäten. Im Jahr 2002 stammten in Estland etwa 97 % der Luftverschmutzung, 86 % des gesamten Abfalls und 23 % der Wasserverschmutzung aus der Energiewirtschaft, die Ölschiefer als Hauptressource für ihre Stromerzeugung verwendet.

Die Ölschieferförderung kann den biologischen und Erholungswert von Land und das Ökosystem im Bergbaugebiet schädigen. Verbrennung und thermische Verarbeitung erzeugen Abfallstoffe. Darüber hinaus enthalten die atmosphärischen Emissionen aus der Verarbeitung und Verbrennung von Ölschiefer Kohlendioxid , ein Treibhausgas . Umweltschützer lehnen die Produktion und Nutzung von Ölschiefer ab, da dieser noch mehr Treibhausgase erzeugt als konventionelle fossile Brennstoffe. Experimentelle In-situ- Umwandlungsprozesse und Technologien zur Kohlenstoffabscheidung und -speicherung können einige dieser Bedenken in Zukunft verringern, gleichzeitig können sie jedoch andere Probleme verursachen, einschließlich der Grundwasserverschmutzung . Zu den Wasserverunreinigungen, die üblicherweise mit der Ölschieferverarbeitung in Verbindung gebracht werden, gehören Sauerstoff und Stickstoff heterozyklische Kohlenwasserstoffe. Häufig nachgewiesene Beispiele umfassen Chinolinderivate , Pyridin und verschiedene Alkylhomologe von Pyridin ( Picolin , Lutidin ).
Wasserprobleme sind sensible Themen in Trockengebieten wie dem Westen der USA und der israelischen Negev-Wüste , wo Pläne bestehen, die Ölschieferförderung trotz Wasserknappheit auszuweiten. Bei der oberirdischen Retorte werden je nach Technologie zwischen einem und fünf Barrel Wasser pro Barrel gefördertem Schieferöl verbraucht. Eine 2008 vom US Bureau of Land Management herausgegebene programmatische Umweltverträglichkeitserklärung besagt, dass Tagebau- und Retortenbetriebe 2 bis 10 US-Gallonen (7,6 bis 37,9 l; 1,7 bis 8,3 imp gal) Abwasser pro 1 Tonne (0,91 t) produzieren. von verarbeitetem Ölschiefer. Bei der In-situ- Verarbeitung wird nach einer Schätzung etwa ein Zehntel so viel Wasser verbraucht. Umweltaktivisten, darunter Mitglieder von Greenpeace haben starke Proteste gegen die Ölschieferindustrie organisiert. In einem Ergebnis legte Queensland Energy Resources 2004 das geplante Stuart Oil Shale Project in Australien auf Eis.
Siehe auch
Verweise
Externe Links
- Ölschiefer. Eine wissenschaftlich-technische Zeitschrift ( ISSN 0208-189X )
- Informationszentrum für die Programmatische Umweltverträglichkeitserklärung (EIS) von Ölschiefer und Teersanden. Bezüglich potenzieller Pachtverträge von Bundesölsandland in Utah und Ölschieferland in Utah, Wyoming und Colorado.
- Die US-amerikanische National Oil Shale Association (NOSA)